Background
Hastings Deering is Australia’s largest Caterpillar dealership supplying Caterpillar equipment to the construction and mining industries throughout Queensland and the Northern Territory.
The major revenue sources comes from after market parts & services.
In 2022 we launched HD360, the Hastings Deering customer platform, with 3 core feature sets.
- Assets: Allowed customers to manage their Caterpillar machine fleet.
- They can see, machine health data, geo location, service history, warranty information
- Finance: Gave customers access to the invoices and credit limit statuses
- Parts Tracker: Track the status of their parts orders
Product Release
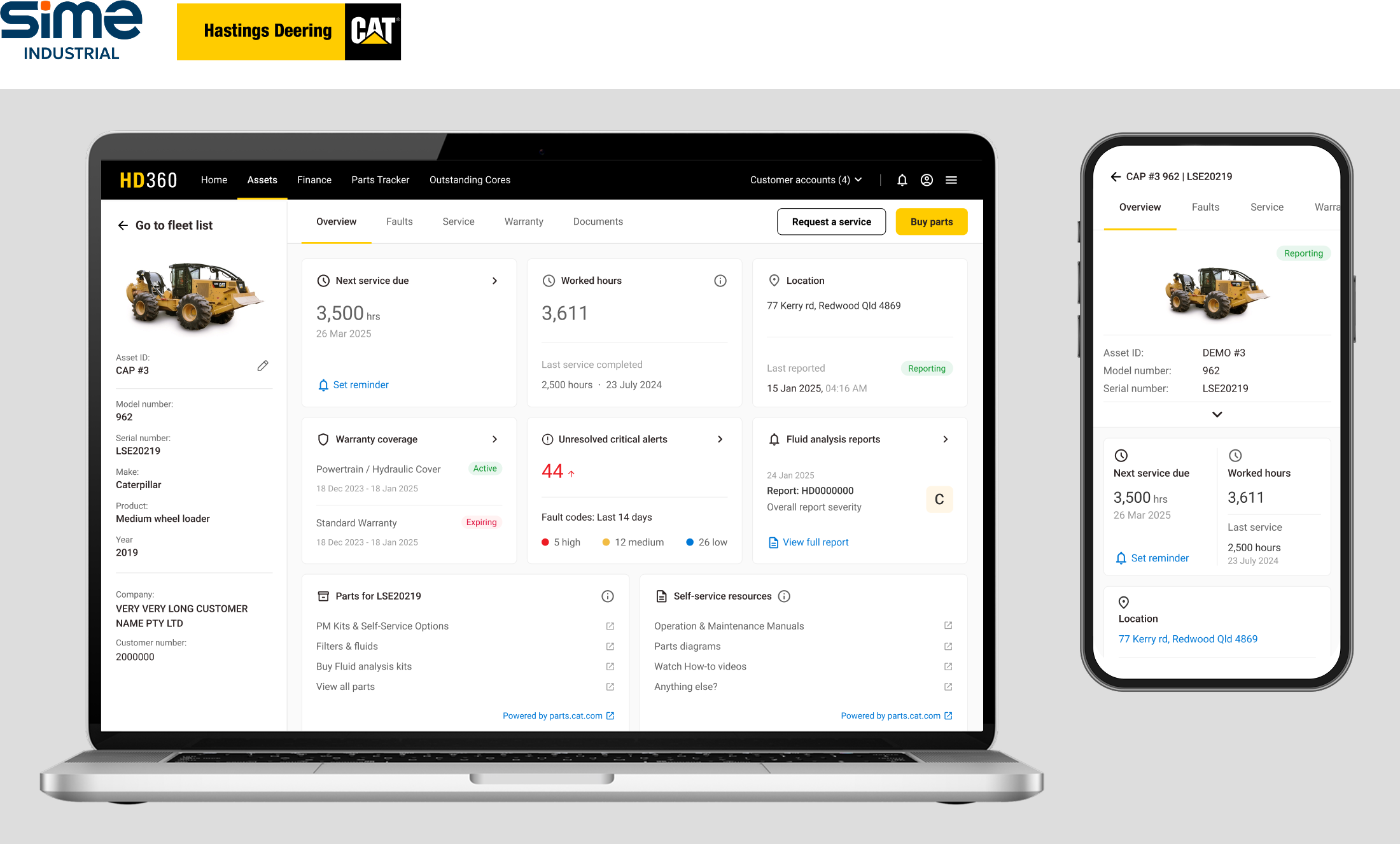
The Challenge
Of the 3 core features in HD360, the Assets section was the feature with the lowest user adoption. The features within the Assets section were basic and we wanted to understand what features the customer would value to get them using this section more frequently.
There was also an opportunity to drive more revenue via the Assets section via parts and servicing.
Original version
When customers click on an asset the first screen they see is the fault codes screen, for many customers the chart would be empty giving a poor first impression.
User Research
Research Goals
A discovery project was created to get a deeper understanding of the value customers were getting from HD360. I wanted to know the following:
- What was working
- What was not working
- What did they find was missing that would get them using the app more frequently.
I lead a team of 3 researchers talking to a diverse group of customers across Queensland, from owner operators with 1 or 2 assets through to large mining companies with 500+ assets in their fleet.
Methodologies used
- 1 on 1 interviews (in person, via MS Teams, phone)
- Focus groups
- Customer support phone data
- Customer feedback via Sales Reps
- Data & Analytics
Research findings
- 60% of customers asked how they can add or remove machines from their fleet list.
- 50% wanted to give their machine s unique ID (nickname)
- Customers struggled to get visibility on their machine service schedule at a fleet level
- Customers wanted to be able to set their own service schedule and get reminders of next service due
- Customers wanted to quickly and easily purchase parts specifically made for their machine.
- Customers wanted quick access to technical manuals for their machine.
- The most valued information in the current feature set was asset worked hours & location. Currently this was buried at the bottom of the left side panel of the asset view screens.
Analysis & Recommendations
After an analysis of the research finding a series of features and or enhancements were recommended to the product owners. These were accepted and went into the roadmap.
Solution
For the redesign I focused on 2 key areas:
- The Assets Fleet list
- Asset Overview dashboard
Updated information architecture
Sketches from a team iteration workshop and the resulting wireframes.
Asset Overview screen (in development)
For the new asset Overview screen, I created a series of snapshots that put focus on things customer told us was important to them. As with the fleet list customers biggest challenge was around servicing their machine.
Highlighting:
- Worked hours
- Next service due date by worked hours & date
- Location
- Warranty coverage, customers always checked this prior to a service so they knew what was they would have to pay for.
- Quick access to parts made specifically for that machine and technical manual for self service.
Booking a service
Adding a booking a service option will allow customers to quickly and easily book a service for their asset. This also helps drive service requests KPIs for Hastings Deering.
Non-connected asset empty state
For a customer to get all the benefits of using HD360, they need to connect their asset to an api that will collect their worked hours, location, machine health issues like fault codes and critical alerts via wi-fi.
The challenge with the Overview screen is that if the asset was not connected, over half the snapshots would be empty.
To address this I created an empty state that included key benefits as to why a customer should connect their machine. Caterpillar also have KPIs on Hastings Deering to increase their connected assets count so this would also address business goals.
Fleet List Enhancements (proposed future state)
Customers told us they wanted a way to view their service schedule at a fleet level, to do this I have added a “Service due date” column to the table data that allowed customers to sort the table by Next service date.
I included a flag next to any dates where the service was overdue as well as the ability to filter the table by “service overdue”.
I also add snapshots across the top to give the customer a quick view on issues that needed their attention should they be limited for time.
Customers will also receive a notification to tell them of upcoming services due for a machine that would also prompt them to book a service with Hastings Deering.
What’s next?
The Assets overview dashboard is currently in development due to release to customers soon.
The final release may differ slightly to screen above.